ホーム > 応援ブログ2014
高トルク対応型のナット。第一工業(株)のネジにかける熱きプロ魂
4月24日(木)、本日最初の取材先は、
第一工業株式会社さん
です。第一工業さんは、今回出展する鋲螺(ネジ)群の他に、教育家具(学校の机や椅子)や、
四輪・二輪などの自動車関連部品を作っている会社です。
本社は浜松市東区にあるのですが、今日は磐田市にある新平山工場にお邪魔させて頂きました。
この工場は1991年に設立されたところなんですネ。(^^)
取材に応対して下さったのは、鋲螺事業部の鋲螺管理課の羽生さんと、技術部開発課の山田さん。
他にも川野参与、石井技術部長、田嶋製造部長と皆さん大勢で迎えて頂きました。
ありがとうございます!大変、恐縮です。(#^^#)
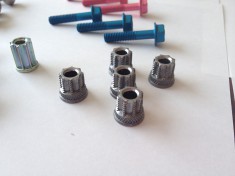
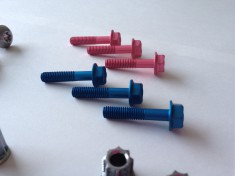
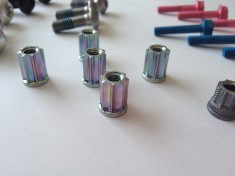
これが、今回の展示会に出展する鋲螺(ネジ)たちです。すべて、手のひらに乗るサイズです。(^^)
左: 高トルク対応型アウトサートナット (手前)
中:高強度アルミニウムボルト(これはカラーコーティングされたもの)
右: 高トルク対応型インサートナット (手前)
高トルク対応型? インサートナット?? 私には知らない言葉ばかりです。(゚△゚;)??
「トルクとはネジを締め付ける力のことを言います。ネジは振動を与えるとどうしても緩んで
しまうので、できるだけ強く締めたいわけです。しかし強く締め付けると、ナットそのものが
回りの樹脂を壊しながら回る現象(供回り)が起きてしまうのです」(羽生さん)
なるほどー、その現象に対応したナットだということですね! (^o^)
では、インサートって何でしょう・・・??
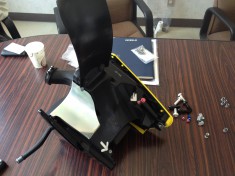
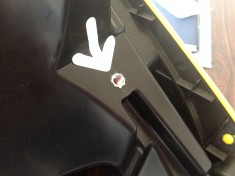
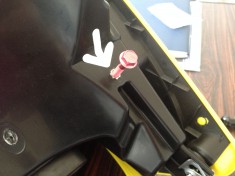
「これがそうです。周りの樹脂を成形する時に同時に埋め込むナットを『インサートナット』と
言います」(羽生さん)
これはバイクの部品でしょうか・・・・?
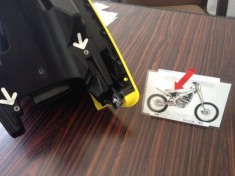
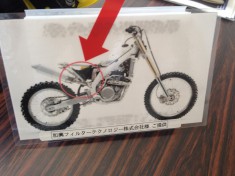
「そうです、ここの部分です」(羽生さん)
あ、そう言えば私も昔バイクに乗っていたので、こういうナットが埋め込まれた部分を
観たことがありますね・・・! (^^;
ところで、社名が出ちゃっていますが、大丈夫ですか? (゚△゚;)?
えーと、和興フィルターテクノロジー株式会社さんですが・・・
「全然問題ありません。むしろ宣伝してくれって言われていますので!(笑)」(山田さん)
「こういう樹脂成形の製品を製作されている会社さんに弊社の技術を見てもらいたいですね」
(羽生さん)
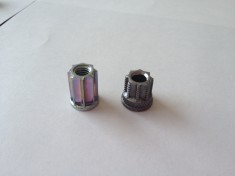
左がインサートナット。右がアウトサートナット。
この8つの襞が、高トルクに対応している秘密らしい。 うーむ。(^^;;
「回転方向に力を分散するために、襞が6つだったらどうかとか、三日月型だったらどうかなど、
この形に落ち着くまでに30~40くらいシミュレーションをしています」(山田さん)
アウトサートの利点は、どういったところでしょうか?
「樹脂製品を成形してから熱を加えながら埋め込む方式を『アウトサート』というのですが、
インサートに比べて人手を介さなくても済みますし、製造ラインさえ作ってしまえば、
自動化(コスト減)に出来ます。ナットが短いので軽量化にも繋がっているのが特徴です」
(羽生さん)
右側のアウトサートナットに見られる、このギザギザはどういった機能を果たすのでしょうか?
「ネジに求められる機能条件は『回らない』と『抜けない(抜け荷重対策)』の2つです。
インサートナット(左)の場合、このフランジ(羽根)が抜けを防止しています。
アウトサートナット(右)の場合、このギザギザが抜けを防止しているのです」(羽生さん)
「形状を決定するまでに、製造側との調整などで3年間くらい試行錯誤があり、決まってからさらに
1年間かかってようやく完成しました。出来上った時は嬉しかったですね」(羽生さん、山田さん)
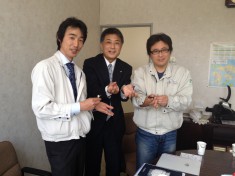
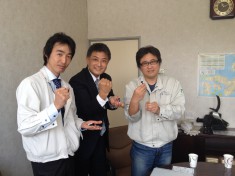
写真左から、羽生卓矢さん、私(小吹)、山田邦男さん。
右の一枚は「恒例の『展示会、頑張るぞ』のポーズ」(^^)
今回の取材の第二部は、工場見学です。貴重な体験をさせて頂きました! (^o^)/イェイ!
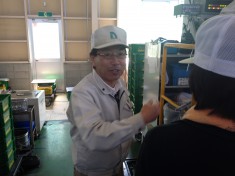
案内して下さったのは、製造部長の田嶋和彦さん。
初心者の私たちに、分り易い解説をして下さいました。ありがとうございます!
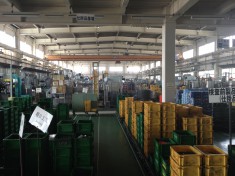
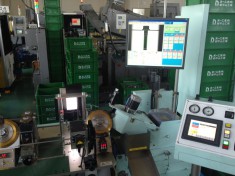
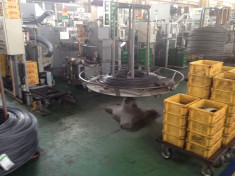
左:工場内はかなり広いです。奥行きが感じられますね。
中:1品、1品画像を撮影しながら検査しているところ。フラッシュが数秒間隔でたかれます。
右:ワイヤーから1つ1つのネジを作り出していて、無駄な端材が発生しないとのことです。
「お客様の要求よりもさらに厳しい基準で検品しています。
100万個に1個のエラーがあっても私たちは許しません」(田嶋さん)
うーむ、さすがプロです! (^^)
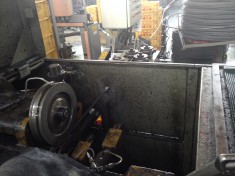
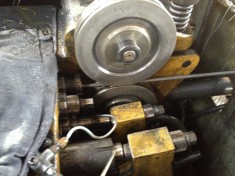
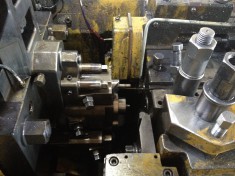
ワイヤーを引き込み、ネジ(ボルト)を成形しているところです。潤滑油の匂いが・・・!(^^;
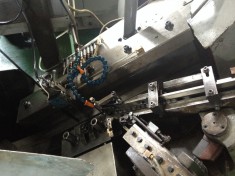
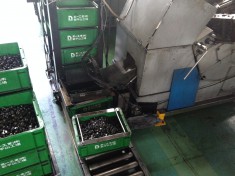
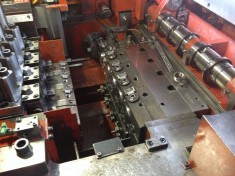
ボルトの場合、『転造』という技でネジの溝が切られます。端材が発生しないそうです。
数も自動的にカウントされ、箱に入れられ、順次送られます。
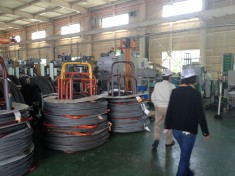
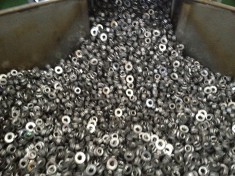
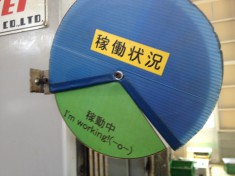
こちらは、ナット工場の様子です。こちらもボルト工場と同様に奥行きがあります。
機械が稼働しているか、一目で分かる工夫が随所にされています。アイム、ワーキング! (^^)
「機械の稼働状況は、遠隔でも管理できます。稼働率を上げることが重要です」(田嶋さん)
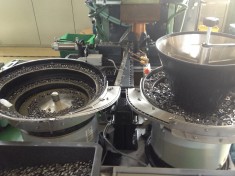
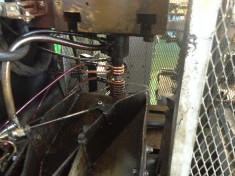
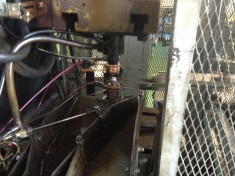
これはキャップナット(袋ナット)を製造している所です。
キャップ部分とナット部分が流れていき、1つずつ溶接されて出来上がります。 プシュー(音)。
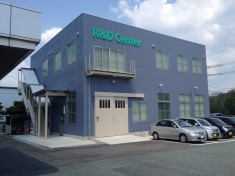
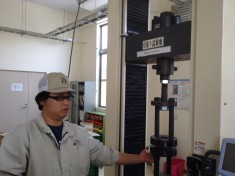
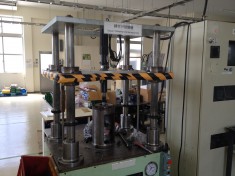
左:敷地内にある、研究開発を行うR&Dセンターです。2012年11月に設立されました。
中:引張り試験機の解説をして下さっている山田さん。
右:締付け試験機。締付けの力の適合範囲を測定しています。
「つまり、お客様にネジを納めるだけでなく、どれくらいのトルク幅で締め付けて頂くかを
納入する際にお知らせしているのです」(田嶋さん)
なるほどー、モノだけでなく使い方まで納品されているのですね! (^o^)
「お客様にとっては『たかがネジ』でも、私たちにとっては『されどネジ』なんですよ」(田嶋さん)
(編集後記)
製品のネジを見ただけでは分からなかったものが工場内にありました。
それは、この1つ1つのネジに込めた「熱きプロ魂」でした! (^o^)/
第一工業(株)の皆さん、大変お世話になりました。ありがとうございました。
企業記事